Chemical Industry
Axalta
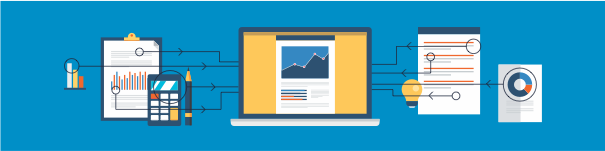
Save energy with intelligent app
Reduce energy costs through the right product
As a car paint manufacturer, Axalta wants to help the body shop to save energy. Most car paints must be dried in an oven at 60°. Axalta also has a product line of extra fast drying products. This can have a major influence on the energy cost of the body shop. In most cases, less energy consumption also means less CO2 emissions. In order to be able to demonstrate this substantial advantage to the body shop, Axalta wanted to have an easy tool developed. This tool should calculate the benefit based on the many parameters influencing the cost such as the type of oven, the ventilation volumes, the ambient temperature, number of cars etc. Parameters that differ from company to company.
Developing an app in the short term
Axalta wanted to respond to the rising energy prices and the attention for reduced CO2 emissions. It was therefore important to develop the tool in very short term. The tool had to indicate how much can be saved on energy costs and CO2 emissions when using Axalta's fast-drying paint. The savings had to be demonstrated compared to other paint products of the manufacturer itself and to competitive products. The online tool was to be used in 35 countries, both by Axalta’s own sales team but also by their distributors.
App calculates energy costs per type of product
Coteng developed a tailor-made cloud application in which the energy cost as well as the CO2 emissions can be calculated. The user can easily enter the parameters for a specific company such as the heating-up time of the oven, the gas price, the air flow, the hourly wage, and so on. If he does not know some parameters, he can use a default. The impact on an annual basis of each parameter change is immediately visible in the graphical dashboard that clearly visualizes the differences between the compared competitive products.
The app goes even one step further. The impact on the productivity of the body shop is also calculated. For example, when a paint product can be applied in fewer layers, it can save on working hours. In combination with the shorter drying times, this ensures that with the same staff and the same infrastructure, more cars can be repaired per day.
The app provides the possibility to test this in practice. The body shop can set up some tests to measure working hours while painting some test objects such as a bonnet with different types and brands of paint. These measured durations are used by the app to calculate productivity differences between the compared products on an annual basis.
This tool is used by Axalta's salespeople and dealers to proof and quantify the benefits of their fast-drying paint for a specific body shop. An extremely important selling point in times of high energy prices.
Handy sales tool
The app has been enthusiastically received by the users. First of all, they only have to enter a limited number of parameters themselves. The Axalta product portfolio and product features (drying time etc) are loaded from existing Axalta databases and kept up-to-date. Other data can be prepared by the administrator of the app on a European level so that the user can easily click on it.
Furthermore, users are guided step by step by a wizard when setting up a comparison in the app. This makes them feel confident in the presence of the (potential) customer.
From idea discussion to final delivery, the development of this app was completed within three months.
Axalta
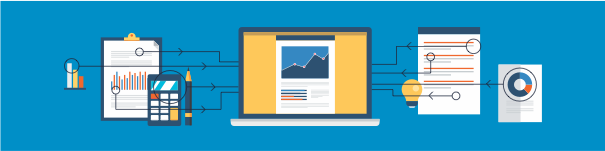
How custom software leads to more productivity
Compose and maintain technical data sheets.
The marketing department of Axalta creates and maintains technical documents/manuals for over 3000 SKUs in 27 languages. All these documents were created and maintained by 4 FTEs.
This was their working process:
- The original version of these documents was always compiled from data and safety phrases from R&D, the pictures came from the marketing department and these data were further supplemented with free text.
- That version was then sent to 27 specialized translators.
- The translated documents were checked for correctness of the data and the layout was adjusted because the translations often turned out to be longer than the original text.
From a manual process to an automated process
Axalta wanted to automate this process in a way that after defining the content of the basic document, no work would be required for translations and control of lay-out. Of course the uniformity and standardization of the end result had to remain guaranteed.
Achieving results with a custom application
We developed a web application (based on a database) that retrieves the necessary data from the R&D database, takes photos from marketing database, uses as many icons as possible and uses standard sentences from a translation database. The application neatly converts all that content into one document with the correct layout for 27 languages
The result is a set of PDFs that nobody needs to check.
- Human work is therefore limited to defining what information must appear in the document.
- When data or photos change over time, the documents are updated automatically.:
- When new sentences prove necessary, translators receive a message and can enter them directly in the translation database.
The productivity improvement is huge.
- There is now only 1 instead of 4 FTEs working on the documents.
- The duration from the introduction of a new document to the final result in 27 languages went from 3 months to 1 day
- Substantially fewer errors are being made in the published documents.
Femail
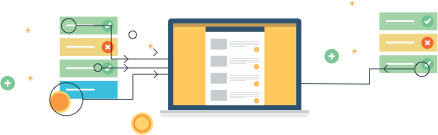
An API platform connects different applications in a cost efficient way
When different systems need to communicate.
Several large companies have presented us with a similar problem in the past. They use different communication systems (e-mail, fax, SMS and others) and different systems for content generation or content archiving. Usually, the need quickly arises to combine the different applications. Connecting such systems one to one results in an exponentially growing number of interfaces.
From one on one to a platform.
Customers wanted a solution that allows to connect the different systems in a more efficient way without sacrificing capacity, speed and reliability.
A modular platform allows unlimited combinations.
A server application was developed that works as a high-speed, high-capacity switching system to store and forward messages. An external system is connected to the switching system by a 'connector' (interface). Once connected, the remote system can communicate with all other connected systems. If a message cannot be forwarded for some reason (eg receiving system not available) it will be send again later. If problems persist, the system administrator will be notified, the message will never be 'lost'. At the same time, a log of all traffic is kept. Connectors are available for many popular communication platforms. If the application to be connected is not included, we develop a connector once.
Some typical examples of connected systems: different e-mail systems, fax, SMS, IBM MQ, application to generate promotional messages , application to generate PIN code, application to confirm appointments via SMS, application to legally archive mails, etc.
Standox
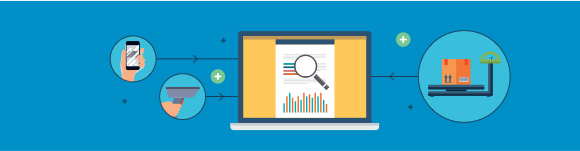
Administrative software leads to significant time saving.
Capture data from different software programs
Sales people at Axalta spend up to 10% of their time making quotes. That is a cumbersome process. These steps are involved:
- These people themselves do not have access to SAP. They have to look up the price information in a spreadsheet (thousands of SKUs).
- SAP uses a different product hierarchy compared to the one used by sales, therefore it is also difficult to search in those list.
- Pictures of the products have to be searched in a marketing database. The copy-paste-method is used to insert them into the quotation.
- Because Axalta products may contain solvents, commercial quotes must also indicate the quantity of solvents contained in these products. This information is to be retrieved from yet another database.
- Finally, the sales person compiles all that information together with an accompanying text in a Word document. Since everyone does this in his own way a uniform layout was lacking in the quotations made.
Process automation ensures ultra-smooth working methods
Axalta asked Coteng to automate the process in order to no longer lose time making quotes.
Simple web-based tool to make quotes, results in more time to focus on sales
A web application sales people can use from any location was our solution.
- The price data are now automatically retrieved from SAP and grouped according to a customer-friendly product hierarchy.
- The accompanying photos are automatically taken from the marketing database and the solvent values from an R&D application
- All this content is then compiled into a single document with a nice layout, following the Axalta house style.
- Furthermore, the application checks whether the sales person adheres to the agreed rules for giving discounts and if necessary his manager is automatically asked to approve an exception.
- When the potential customer approves the quotation, the prices with corresponding customer-specific discounts are loaded into SAP.
Axalta
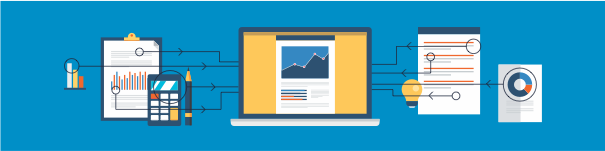
Smart application boosts productivity
Collect data and calculate KPIs
As a car paint supplier, Axalta helps bodywork companies to improve their productivity. This requires a lot of data to be collected about the daily operation of the company: working hours per repair, consumption of paint and other goods needed for the repair. Once these data have been collected, a number of KPIs can be calculated that indicate where improvement is possible. For a consultancy service, providing such a service is a time-consuming and expensive matter that needs to be repeated regularly to be effective.
Develop a method to evaluate productivity continuously
The development of a solution that allows the owners of bodywork companies to permanently evaluate productivity / profitability.
Web application maps business processes in real-time.
We developed a web application that:
- registers working hours per vehicle via barcode scanning or manual entry per task (cleaning, sanding, primer, etc.).
- keeps track of paint consumption per vehicle via scales and / or manual input.
- keeps track of the consumption of other goods via scanning or manual entry (tape, sanding paper, masking film, etc.) per car.
The application allows the owner to monitor and manage the processes in his business in real time. There are always a number of predefined KPIs available (numerically or graphically) so that the owner knows where adjustment is needed.
Wind Energy
Otary
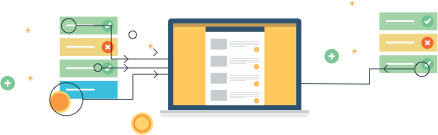
Offshore wind turbine maintenance planning application integrates AI model and various data sources into a useful tool for the planner.
Decision tool for maintenance offshore wind turbines
Automation of the planning process
Wind farm operator Otary wants to make the planning of its offshore wind turbine maintenance more efficient and automated. The planning is now being done in a spreadsheet based on various factors that can influence maintenance such as availability of parts, a vessel or technicians with the right skills, the weather, the type of work, the distance the vessels have to travel and so on. The planner must therefore consider many factors that, additionally, change over time. Often, these parameters have to be searched in disparate systems. By developing a customised tool, most of the processes and calculations can be automated and the planner's work can be simplified. The planner can then concentrate on defining the balance between these factors - the system will optimize to that balance.Recently, Otary developed an AI model that predicts the expected energy production per wind turbine at a particular time based on the weather forecast. Production actually varies for each wind turbine depending on its positioning and wind direction. The AI model generates this data 4 times a day based on the latest weather data for the next few days. Depending on the type of maintenance, the wind turbine has to be shut down for a short or longer period of time. By tailoring a planning tool, this parameter can be taken into account to integrate the loss of electricity production in finding the balance between the various factors.
Since weather forecasts are constantly changing, an optimized plan is not necessarily the most optimal at the next forecast update. Automation allows more parameters to be taken into account and still have ‘up to date’ plans at all times. Such optimization work cannot be sustained manually.
The aim of this project is to develop a smoothly working dynamic tool for the planner that combines all data, automates calculations and updates as soon as new data are available.
Digital twin
Initially, a proof of concept will be set up in a relatively short period of time (3 to 4 months). That way, the user experience can be evaluated in order to work out the next steps.
We set up a web application that collects data from different sources and presents them in a user-friendly interface that allows the planner to simulate different scenarios or start an optimization process. The heart of the application is a digital twin of the wind farm that simulates the output of the farm per wind turbine based on all the parameters set by the planner.
Based on the meteorological forecasts and the predicted production, different parameters are used to determine which wind turbines can undergo the specific maintenance task. For this purpose, the three offshore wind farms Mermaid, Seastar and Rentel are visualized with their respective wind turbines. The tool takes into account factors such as the type of maintenance work (e.g. painting or working on the turbine), the time of day and the production capacity at that time. On this basis, the tool visually shows the wind turbines that can be worked on and those that cannot. The reasons for rejection can be consulted. The tool is fed with accurate info 4 times a day (every 6 hours).
Smart tool for planner
The tool has been enthusiastically received by the planners. The combination of several factors in the same tool provides great user convenience. At a glance, he can consult clear and accurate information to make decisions. As a result, he saves significant time and human error can be reduced. The measurable results of the tool will be announced in about six months' time.
‘This tool, developed by Coteng, has the potential to become the ideal co-pilot in offshore planning’ - Katja D'haeyer, data scientist at Otary
Optimisation tool for maintenance offshore wind turbines
Priority versus regular maintenance work
Otary wants to maintain its offshore wind turbines according to an optimally well-organized system. There are, in fact, many different maintenance activities required on a wind turbine. What is possible on a given day also depends on the skills available on a ship. Some work is done only yearly or occasionally, while other tasks are high priorities. A working day is composed of priority tasks and completed by other tasks. Otary requires a planning tool that allocates these two types of work to a given team according to a well-defined logic and optimized to the requested balance between the various parameters.Optimizing maintenance tasks with digital toolCoteng is building a tool to plan maintenance tasks. The tool defines the available team with the right profile on a given ship. They are linked to a certain urgent task (= MUST task). The working day is completed with less urgent tasks (= MAY task). This optimization tool uses the data generated by the decision tool (see above). This means that the maintenance works are carried out only on those wind turbines that fit the balance between the different parameters requested by the planner.
Furthermore, the planning takes into account, among other things, the travel time to the wind farm, the expected duration of the maintenance works, the time needed to load equipment, and so on.
Increasing efficiency
The combination of several factors in the same tool ensures great convenience. The planner can consult clear and accurate information from a quick scan to make decisions. When new data become available, plans and calculations are automatically updated. The results of the tool are measured and evaluated after a 6-month implementation period.
These tools were fully developed in 6 months, from draft to running model in production. After evaluating the user experience over a longer period, the tools can be further expanded with additional functionalities.
This project is part of the ELBE EUROCLUSTER project (GA- 101074230), which received funding from EISMEA's COSME program (call SMP-COSME-2021-CLUSTER).Funded by the European Union. However, views and opinions are solely those of the author(s) and do not necessarily reflect those of the European Union or EISMEA. Neither the European Union nor the funding body can be held responsible for them.
Parkwind
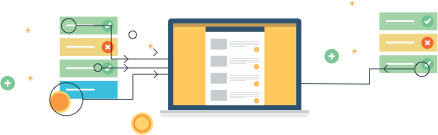
Automation for the calculation of the Green Power Certificates (GPC)
Processing data for the application of the GPC
Parkwind builds and operates offshore wind farms. In addition to electricity, these windmills also generate a constant stream of data. This data stream can deviate due to various causes. For example, a broken sensor, or maintenance work or simply a counter that has reached its maximum and jumps back to zero.
Until recently, Parkwind used standard software to process the data for the application of Green Power Certificates (GPC). Loading the data, correcting anomalies, and start processing took their engineers quite a bit of time each month. Moreover, those actions were also very susceptible to human error.
Process data streams efficiently
Cleaning and processing the data stream taking into account all possible deviations and exceptions giving the engineers a noticeable time saving. In other words: efficient data processing.
Automation delivers significant time savings
Initially, AI was considered to work with. But after further analysis with the engineers, it turned out that the anomalies were easily identifiable. AI only makes sense when the logic between input and output is not clear. It also requires a huge amount of historical data for the model to 'learn'. Therefore, we decided to do things differently. First, we defined all possible deviating scenarios. Subsequently, we built custom software that knew what to do in case of any deviations. As a result, the Green Power Certificates are automatically requested to the government.
Ultimately, this automation saves Parkwind 2 to 3 days of manual and repetitive work every month. The GPCs are approved faster because human error is excluded. The engineers are happy to be relieved of this monotonous task while maintaining control.
Banking Industry
BNP Paribas Fortis
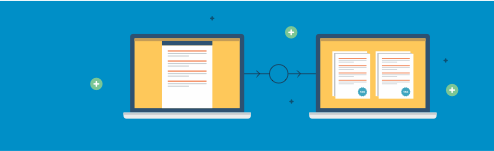
Powerful app is the solution for mandatory data archiving
New legislation requires new communication flow
BNP Paribas Fortis has been working for years with a customized communication gateway from Coteng. This ensures the integration of various business applications that are directly or indirectly related to e-mail, fax and SMS. Since 2018 it is mandatory for financial institutions, in the context of MiFID II, to archive a copy of all personalized publicity. The system the bank used to send publicity via e-mail does not have that possibility.
Data processing and storage in a user friendly format.
The bank asked us to archive the emails in a generally supported format that can display e-mails as they were shown to the customer. Tags had to be added to this to make searching in the archive possible. Such publicity campaigns often generate tens of thousands of e-mails per hour. To process these flows a high-performance application is required.
Extension to existing application provides data archiving conform the legislation
Modules were added to the existing gateway to convert outgoing e-mail messages with personalized publicity into pdf format and add the necessary tags (campaign, customer, ...). These files then are delivered to the standard application that archives them as prescribed in the MiFID II legislation.
Startups
Parlangi
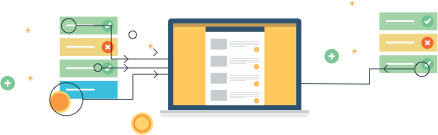
From startup prototype to a professional platform
User-friendly platform for young and old
Parlangi connects people, more specifically 'junior' non-native speakers are brought into contact with 'senior' mentors who speak their mother tongue. The junior learns the language in a relaxed atmosphere and the mentor has useful social contact.
Initially, Parlangi approached Coteng as a startup. They wanted to offer seniors a user-friendly platform with video connections. In addition, junior and mentor would be linked via a database based on language and interests. And, users should be able to easily schedule video sessions in an online calendar. The challenge was to achieve this with a very limited budget as is characteristic of start-up companies.
Flexible architecture, to adjust and scale up
In a first step, it was important to try out the concept with real users. We have set up a prototype. In startup projects, it is important to design a flexible architecture. This way you can adjust the product after feedback. As the startup grows, the system must be scalable over different servers.
In this project, we worked with existing libraries in order to keep the development costs limited. For Parlangi it was important they became the owner of the source code and they could actively manage some parts themselves. Currently, a number of pages are managed by Parlangi.
Cost-efficient growth
With the feedback of the prototype, the current version of the user interface was designed and implemented. This version had to ensure that both the older and younger generation could work smoothly with the platform. A number of specific components have been custom-made for this.
Due to the well-thought-out architecture, more features could gradually be added as the experience and budget grew. In this way, the platform could be further expanded for other target groups. Both the VDAB (i.e. a Flemish employment agency) and various municipalities have recently started to use the Parlangi platform for their integration and language programs. For this purpose, we have added a dashboard module in which a coordinator can monitor the progress of the participants.
Because not all seniors have access to a computer and students nowadays prefer to work with mobile phone or tablet, there is also an iOS and Android version of the application available.
For more info about Parlangi: www.parlangi.net
Digital signage
Quick
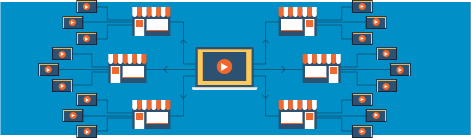
Custom web application integrates marketing communications
Different systems per location
The menu and publicity screens, promotions and music in the restaurants were controlled by different systems and had to be handled by the local restaurant.
Automatic control from a central point
Quick was looking for an integrated solution in which all screens and the music in the restaurants (individually or in group) could be directed from a central point via internet. The content had to continue to play autonomous also when the internet connection would be lost.
Time saving and uniformity with custom software
Coteng developed an application for the central marketing department.
Via this application the user:
- can determine what should be shown on a certain screen, in a certain restaurant, at a certain time with or without sound / music
- can plan videos, photos, presentations, live images, scrolling text or combinations thereof.
In this application the different types of content and the music are combined into a playlist that can be previewed immediately and can be published in a schedule per week.
To prevent screens going black when the internet connection drops out - what happens with traditional streaming technology - content for a full schedule on the local screens are buffered and repeated until new content is available.